Generalized Biomanufacturing Platform - Update from ASLS + GE Healthcare Life Sciences
- Advanced Solutions
- Nov 19, 2018
- 1 min read
Updated: Jun 10, 2020
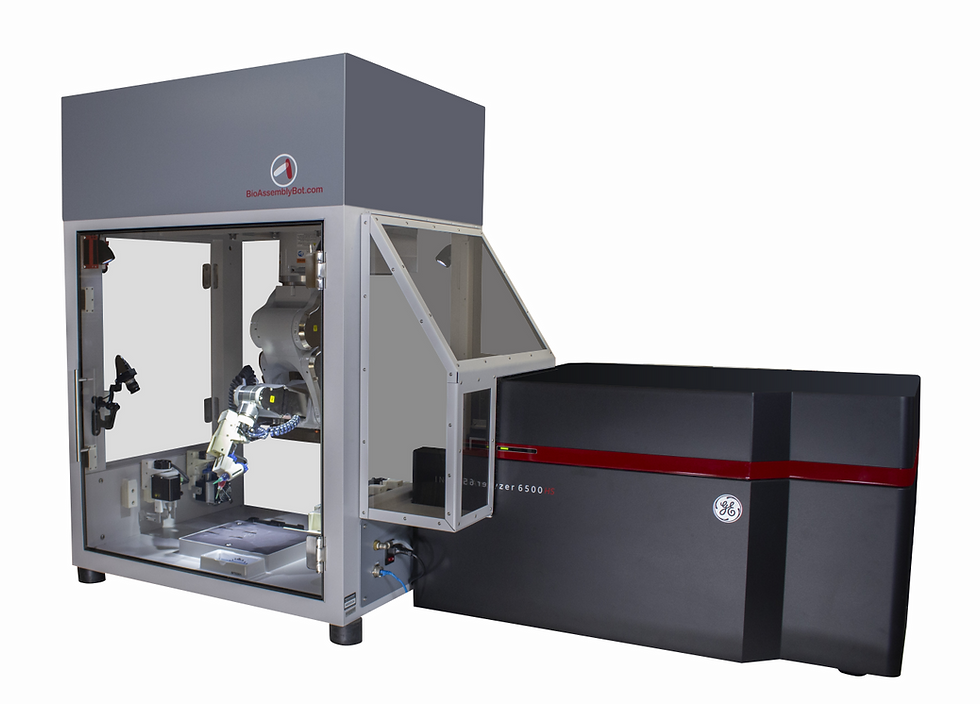
“Generalized Biomanufacturing Platform for Dynamic Vascularized Tissues,” proposes the development of a manufacturing workflow solution for the building of vascularized tissue that is suitable for use in clinical applications and non-clinical commercial spaces. The technical approach of this project involves the development and integration of task-specific controls within existing equipment, in combination with new manufacturing tool sets and microfluidic capabilities, to create a vascularized tissue.
Renowned for their 6-axis robotic bioprinter/biofabricator, also known as the BioAssemblyBot® (BAB), ASLS has partnered with GE HLS to combine their respective technologies to advance the capabilities of the BAB to include multiple automated workflow capabilities, elevating tissue fabrication from a laboratory phenomena into a manufacturing process. Jay Hoying, Partner and Chief Scientist at ASLS and Project Lead, states “The motivation for the project really speaks to the broader mission that we had at ASLS for tissue manufacturing, which ARMI helped to crystallize. The Bio-Assembly® platform that we currently have, while it does tissue printing, was envisioned to be an automated tissue engineering platform.”
The printer features a six-axis robotic arm, which allows for precise printing of complex 3D tissue components, with additional degrees of freedom for movement on both planar and non-planar surfaces. It is ideal for printing cell systems and 3D assays, experimental tissue models and microenvironments, organ models, microfluidic platforms, implant systems, and many other structures.
Comments